Mobile Instandhaltung 4.0:
Vernetzung, Smart Objects, Production, Maintenance
Industrie 4.0 ermöglicht vorausschauende Instandhaltung/ Predictive Maintenance. Um Störungen und Ausfälle vorhersehen zu können, muss die Maschine vernetzt sein, damit Sensordaten von Schlüsselbauteilen kontinuierlich abgefragt und ausgewertet werden können. Ziel der Predictive Maintenance ist die Reduzierung von Stillstandszeiten, die Reduzierung von Wartungsintervallen und die optimale Nutzung des Verschleißvorrates.
Abgrenzung, Industrie 4.0 in Produktion und Instandhaltung: Während die Produktionsleitebene Sensoren abfragt, die Produkt, Produktionsfortschritt und Qualität überwachen, fragt die Instandhaltungsebene Steuerungsdaten, Sensoren/Smart Objects ab, die den Maschinenzustand überwachen. Das sind zumeist Schwingungs-, Wärme- oder Drucksensoren an Walzen, Motoren, Spindeln oder Flüssigkeiten. Die Sensordaten werden in Auswertesysteme eingelesen und dort nach Grenzwerten und Trends bewertet. Von allen Messungen gehen nur die auffälligen weiter an den Instandhaltungsleitstand, wo Maßnahmen für jede kritische Abweichung hinterlegt sind.
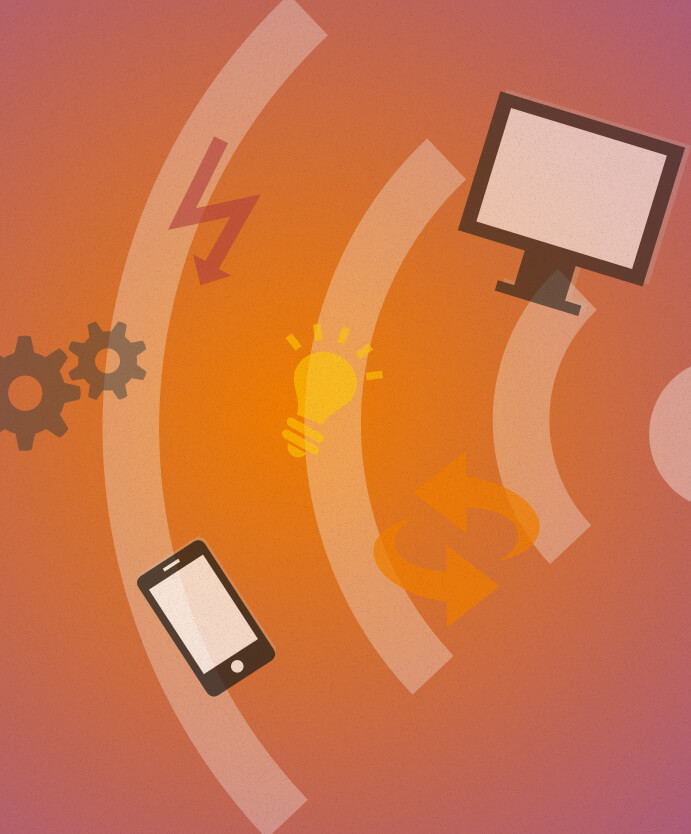
Instandhaltung 4.0
Ein modernes Instandhaltungsmanagementsystem bindet die Instandhaltungsebene ein und vernetzt den Leitstand mit dem Menschen und mit anderen Systemen wie Lagerverwaltung oder Zulieferer. In der Praxis gibt der Dispatcher am Leitstand z. B. Ersatzteilbedarfe an das Lager weiter. Der Instandhalter erhält seine Tagesmaßnahmen auf sein Mobile Device, der Instandsetzer wird genau an die richtige Stelle an der Anlage geschickt. Der Maschinenhersteller erfährt automatisch von den Störungen, die er beheben muss, und der Servicepartner erhält automatisch Serviceaufträge, für die er vertraglich verantwortet wurde.
Paradigma bietet dieses System mit den ASSIST | MODULEN in verschiedenen Ausbaustufen.
die Details
- MACHINE | ASSIST: Asset LifeCyle Management-Leitstandsoftware für die Verwaltung von Sensorikmaßnahmen und klassischen, zyklischen Instandhaltungsintervallen nach Stückzahl, Maschinenlaufzeit, Echtzeit, Durchflussmengen mit Schnittstellen zu Anlage und Steuerung.
- MRO | ASSIST: Instandhaltungsstartszenario: Mit Auslieferung der Anlage gleichzeitige Übergabe aller Instandhaltungsmaßnahmen, Maßnahmen für Fehler- und Sensormeldungen für das Einlesen in ein Instandhaltungsmanagementsystem. Dieser Maintenance Digital Twin ist das Instandhaltungs- oder Maßnahmenstartszenario.
- Anpassung des Maßnahmenstartszenarios durch den Betreiber zur Optimierung der Intervalle, abhängig von Auslastung, Belastung und Peripherie seiner Anlage.
- MACHINE | ASSIST:
PULL: Download aller Maßnahmen vom Leitstand als Tagesvorrat auf Smartphone oder Tablet, Rückmeldung aller Arbeiten an den Leitstand.
PUSH: Übermittlung von Störungen an das Mobile Device zur schnellen Fehlerbehebung. - Historie zu allen Arbeiten